We are presented with a request for quote for IP69K testing on a regular basis at F2 Labs. Usually my first reply to the customer is this, “Do you mean IP69 or IP69K?” Believe it or not, there is a difference and it is an important distinction. This article will explain.
Before we get into the details, the most general distinction is that IP69 testing is for equipment, like control panels or electrical equipment that is installed in areas that get washed (pharmaceutical manufacturing, industrial food packaging), and IP69K is for equipment installed on road vehicles. And the IP69K testing is meant to validate that the equipment installed in road vehicles can withstand very severe wash-downs with pressure washers.
IP69 is the IP (ingress protection) code for a very high level of protection as indicated in IEC 60529 – Degrees of protection provided by enclosures (IP code).
IP69K is the IP code for a very high level of protection as indicated in ISO 20653 – Road vehicles – Degress of protection (IP code) – Protection of electrical equipment against foreign objects, water and access.
First, I want to share the full chart from IEC 60529, clause 4.2 below –
4.2 Elements of the IP Code and their meanings
A brief description of the IP Code elements is given in the following chart. Full details are
specified in the clauses indicated in the last column.
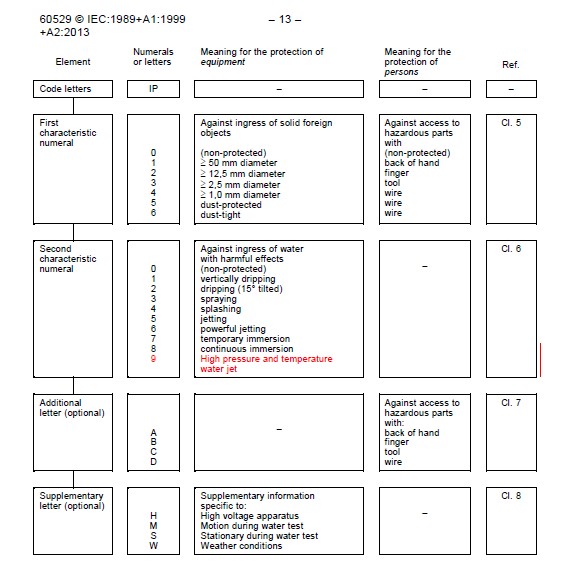
Notice there is no reference to any “K” test or designation anywhere in the chart. It does not exist in IEC 60529.
The IP69 testing consists of a dust test (IP6X) and a water test (IPX9). See this previous article for more information regarding IEC 60529 testing.
Link – IEC 60529 testing article
As pertains this article, we want to investigate the differences between the IPX9 testing from IEC 60529 and the IPX9K testing from ISO 20653.
The IPX9 test from IEC 60529 is indicated in clause 14.2.9 and is below –
14.2.9 Test for second characteristic numeral 9 by high pressure and temperature water jetting The test is made by spraying the enclosure with a stream of water from a standard test nozzle as shown in Figures 7, 8 and 9.
The set-up for measuring the impact force of the water jet is given in Figure 10.
The distribution force shall be verified at upper and lower limits of distance tolerance range (see Figure 11).
a) For small enclosures (largest dimension less than 250 mm), the enclosure shall be mounted on the test device shown in Figure 12.
– turntable speed: 5 r/min ± 1 r/min
– spray positions: 0°, 30°, 60°, 90°
The test duration is 30 s per position.
b) For large enclosures (largest dimension greater than or equal to 250 mm), the enclosure shall be mounted as per intended use. The entire exposed surface area of the enclosure shall be subjected to the spray at some point during the test procedure.
– spray positions: the enclosure shall be sprayed from all practical directions covering the entire surface area and the spray shall be, as far as possible, perpendicular to the sprayed surface.
– distance between nozzle and sample under test shall be 175 ± 25 mm.
The test duration is 1 min/m2 of the calculated surface area of the enclosure (excluding any mounting surface), with a minimum duration of 3 min.
Next, we will review the correlating chart in ISO 20653. See Table 1 in clause 4.2 below –
4.2 Meaning of IP code
Table 1 contains an overview of the IP code elements.
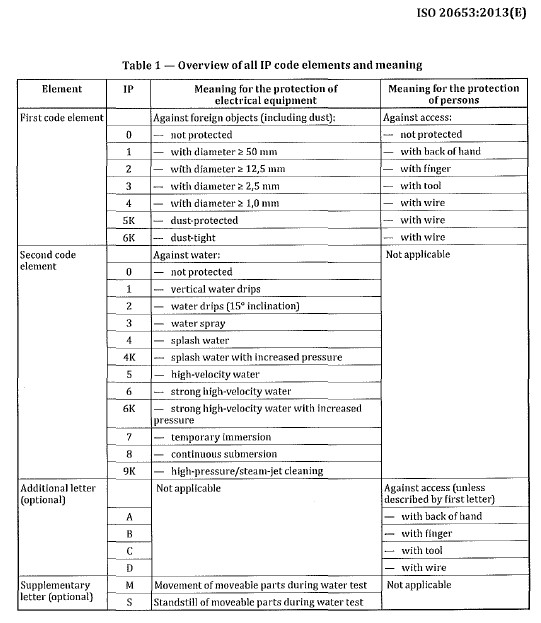
We notice right away that there are several “K” designations in the above table – IP5KX, IP6KX, IPX4K, IPX6K, and IPX9K. (Note that the inserted “X” means the correlating water or dust test from the string is not considered. For example, IP5KX means that there is 5K dust test but no water test is indicated.)
There are no “K” designations in the table from clause 4.2 of IEC 60529.
Since most requests we receive with a “K” at F2 Labs are for IP69K, we will investigate the IPX9K test from ISO 20653 and compare it to the IPX9 test from clause 14.2.9 of IEC 60529.
We will review Table 7 in clause 9.2 of ISO 20653 to understand the test conditions/ protocol for IPX9K –
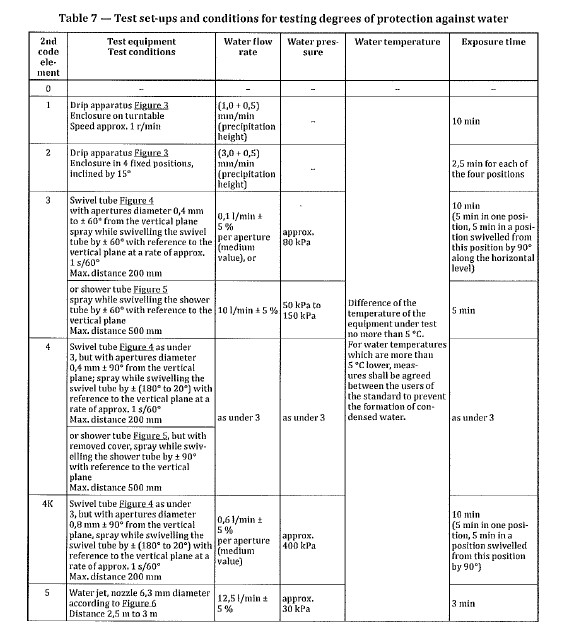
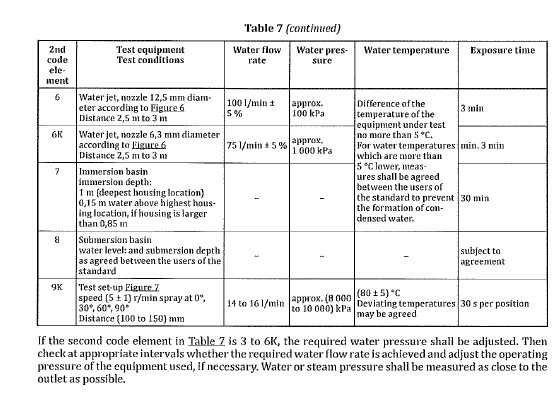
Let’s get a close-up of the 9K test –

Since we have laid out both test procedures (IEC 60529 IPX9 and ISO 20653 IPX9K) next we will make a direct comparison, see below –
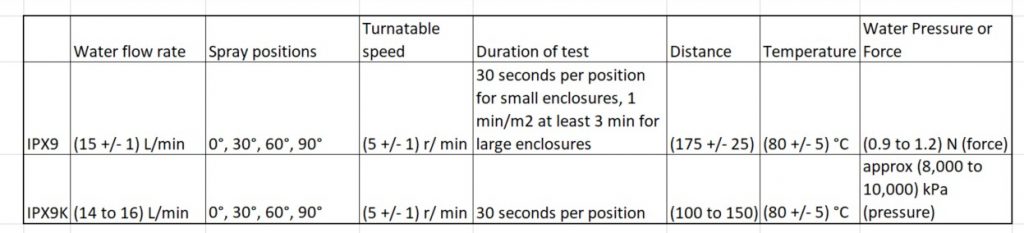
Some notable differences are:
- The distance for the test nozzle for the IPX9 test is 175 mm, plus or minus 25 mm and the ISO IPX9K test is 100 to 150 mm.
- The impact of the water is measured in terms of force for the IPX9 test while it is measured in terms of pressure for the IPX9K test.
The tests are different.
Adding to the confusion, there appears to be a typo in IEC 60529 standard that has caused some headaches (and probably not only here in our lab!). IEC 60529 was written in French and the standard, when purchased, typically comes in French and English in the same document.
See clause 14.2.9 in the English part of IEC 60529 –
Now see clause 14.2.9 in the French part of IEC 60529 –
Since we are all busy and this article has become long enough, I will show you what the discrepancy is. There is a sentence about temperature in the French section that is not in the English section. See below –
I do not speak French, but Google tells me that the sentence translates as follows:
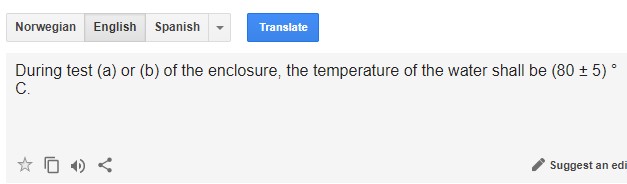
So, this validates that the temperature requirement is the same for IPX9 and IPX9K testing.
Continuing, I have been asked on a few occasions to quote an IP69K test for a product based on the German standard, DIN 40050-9 – Road vehicles; degrees of protection (IP-code): protection against foreign objects; water and contact; electrical equipment. DIN is the German Institute for Standardization.
Please see below the WITHDRAWN status of DIN 40050-9, as indicated on the DIN site –
Summarizing all of the above, please see below –
- IP69 is testing from an IEC standard and is for electrical equipment while IP69K is testing from an ISO standard and is for electrical equipment mounted on road vehicles.
- IP69 testing requires that the FORCE of a water jet is measured during the water test while IP69K testing requires that the PRESSURE of the water jet is measured during the water test.
- The distance of the water jet nozzle can be up to 50 mm further away for the IP69 water test (200 mm) as compared to the IP69K water test (max distance is 150 mm).
- Frequently DIN 40050-9 is indicated as a rationale for requiring IP69K testing. DIN 40050-9 is not an active standard.
F2 Labs is here to help.
Have a question or a comment? We can be contacted via this link. We can be reached by phone at 877-405-1580 and are here to help you.